Potential danger of cone crusher.so what can we do in crusher repairs ?
Minor repairs
The minor repairs is usually conducted 15-30 days, and the main contentsinclude:
1) inspect the wear of spherical bearing, taper sleeve, eccentric sleeve, base bushing, bottom end bearing, bevel gear, dustproof and sealing device, and adjust their coordination;
2) replace or adjust the spring of the frame;
3) fasten the bolts of each part;
4) cleaning, checking oil circuit and cooling and dustproof water system, eliminating oil leakage, adding or replacing lubricating oil, repairing oil pump;
5) inspect the wearing condition of the umbrella board and each part of the fender;
6) check the transmission bearings (bushings) clearance and momentum, if necessary, replace;
7) cleaning, refueling of motor and bearing.
General repairs
The general repair is usually conducted every 4~6 months, and the main contents include:
1) replace the lining board;
2) repair or replace eccentric shaft sleeve, taper sleeve and straight sleeve;
3) repair or replace the bowl and dustproof device;
4) repair or replace bevel gear, transmission shaft and bearing bush;
5) repair the adjusting ring and supporting sleeve thread;
6) all the inspection of the repair project and treatment;
7) decompose motor, blow dust, scale and check the gap of each part bearing; decompose oil switch, clean and deal with the defects; adjust and test the electric adjustment of each part; check and repair the switchboard and other cable.
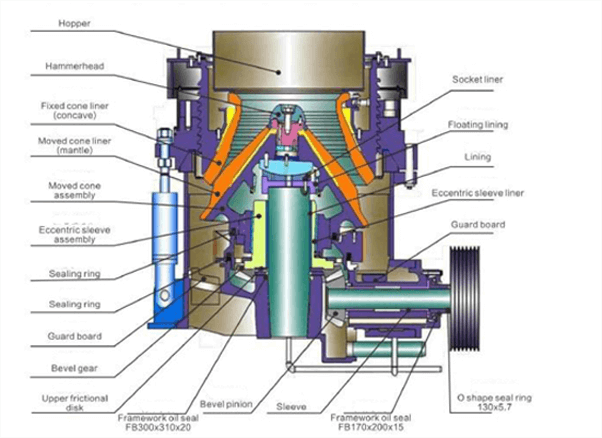
Overhaul
Overhaul, general 3-4 years, or according to the specific situation of crusher production, the main contents include:
1) all disassembly inspection of cone crusher, adjust gear meshing clearance, check or replace the upper, middle and lower round plate;
2) change the movement and fix the lining board;
3) replace taper sleeve, base bushing, size bevel gear, transmission shaft, etc.;
4) scrape spherical bearings or replace and weld spherical bearing housings;
5) welding supply hopper, shield, body guard board, etc.;
6) replace part or all base spring and spring bolt;
7) replace the oil pump. High frequency small, users in the production according to the specific circumstances extended to 1-2 months. Timely maintenance will help clear the hidden problems in the equipment, and lay the foundation for efficient production.